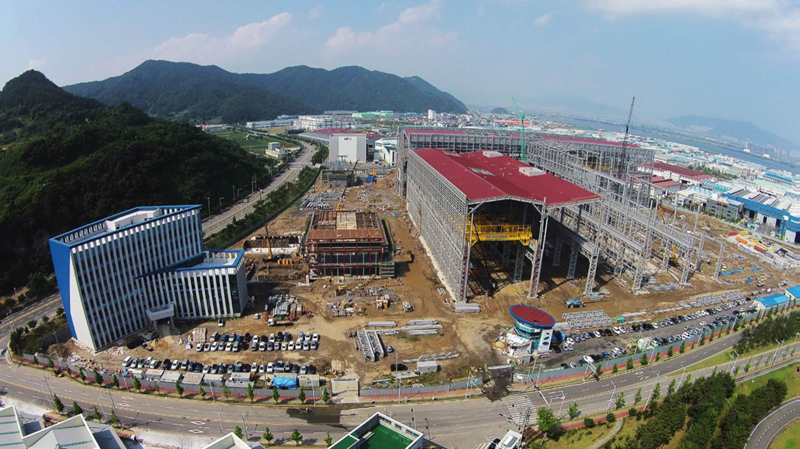
Manufacturer uses Tecnomatix to complete feasibility study for steel mill retrofit within two months
Siemens solution enables Inteco to enhance customer confidence and boost readiness to accept plant orders
Full custom steelmaking equipment
Steel is an integral part of the global economy and one of the most common manmade materials in the world, with more than 1.6 billion tons produced annually. Although iron is quite ductile, removing impurities and adding small amounts of elements such as manganese, nickel, chromium, carbon and vanadium as hardening agents turns it into steel. In primary steelmaking, liquid iron and steel scrap are turned into steel in LD Converters or electric arc furnaces. In secondary metallurgy, alloying agents are added, dissolved gases in the steel are lowered, and inclusions are removed or altered chemically to ensure high-quality steel production.
With a workforce of 200 in Austria as well as another 200 spread across subsidiaries in Brazil, China, India, Italy and the United States, Inteco offers highly automated solutions for individual plant sections as well as complete plants tailored to customers’ requirements. What sets the plant creators apart is their know-how and experience not only comprise mechanical, electrical and process engineering, but also metallurgy.
– All that customers need to specify is exactly what steel grade they plan to produce, says Herwig Brauneis- Weber, head of quality management, Inteco. That is all we need to determine the optimal plant design. Although other plant creators have a limited choice of plant section sizes, Inteco’s flexibility allows full custom plant design.
In pursuit of the digital twin
The Inteco experts engineer the secondary and special metallurgy equipment from scratch every time, including mechanical, electrical and software design. They use dedicated software solutions for the various tasks, including mechanical and electrical computer-aided design (ECAD). They use COMOS software from Siemens AG for computer-aided engineering (CAE) as well as operating and maintaining process plants they create.
– In the CAD environment, the simulations only included the parts of the plants we created, says Bernhard Köller, quality management and simulation expert at Inteco. Ruling out collisions worked well but we were unable to include external factors such as the buildings.
For project management work and production engineering, the Inteco experts used to work with spreadsheet software as well as visualization and presentation office software.
– This was less than satisfactory because it did not support coordination with customers, says Brauneis-Weber. Beyond a certain size and complexity of a project, it was really difficult to keep track of all the information. No wonder they had nicknamed the extensive spreadsheets “shrouds.”
At the same time, customers more frequently demanded studies such as a ladle swapping time analysis, which goes beyond what is practically feasible using spreadsheets.
– A major U.S steelmaker intending to refurbish an aged steel mill required a logistics study with an as-is analysis as well as a feasibility study, including a monetary proposal for the investment, says Köller. This prompted us to look for a more appropriate solution.
Tecnomatix for plant simulation
The steelworks experts found the simulation solution they had been looking for in the form of the Tecnomatix portfolio, a comprehensive group of software solutions from Siemens Digital Industries Software for the digital factory. Tecnomatix can be used to cover all aspects of production, from process definition, planning and simulation to verifying all production steps and using the digital twin in subsequent operations. To facilitate an easy information exchange with other product data sources, Tecnomatix uses the Teamcenter software manufacturing backbone as a foundation for product lifecycle management (PLM). This allows seamless transition of information from product design to manufacturing to logistics.
The Tecnomatix software training the Inteco experts took was carried out by HATEC, a Siemens Digital Industries Software solution partner. Specializing in plant simulation and offline robot programming, the company has been using various products from the Siemens’ Tecnomatix software portfolio since 2002.
– This allows the seamless development of production solutions from ideation to simulation to virtual commissioning, saving our customers unpleasant surprises and unpaid expenses, says Jens Kraiger, chief executive officer (CEO). The initial investment in a complete definition and model creation pays off very quickly. Kraiger’s father had founded the company to promote virtual commissioning because he was weary of spending weeks in half-finished buildings in the middle of nowhere.
Supporting simulation
– During our training, we were pleasantly surprised to see how fast we got the hang of Tecnomatix, says Köller. As we were also impressed by HATEC’s enormous expertise and experience, we decided to cooperate with the simulation experts.
The nature of the cooperation is that Inteco defines the plant and provides the layout data from their CAD software as well as parameters such as material quantities, batch sizes and cycle time. HATEC builds the dynamic model and does all the required programming. The first joint project was the feasibility study for the aforementioned American steel mill retrofit.
– From our initial one-day meeting with HATEC we returned with a complete draft concept, says Brauneis-Weber. Within only two months this turned into a full-blown logistics and feasibility study.
Starting with the requirement specification and the findings of the as-is analysis, the study covers all aspects of steel production after the retrofit. Its output formats include GANTT charts as well as analyses in the shape of Excel spreadsheet software. HATEC supplied the study in a ready-to-use digital form.
– It includes a user interface so the customer can modify parameters to try out various scenarios, adds Brauneis-Weber.
Moving toward digitalization
Within the large and complex plants the Inteco engineers design and build, the material flow is a key success factor. According to Köller, a main benefit of simulation-based plant engineering using Tecnomatix Plant Simulation is the opportunity to optimize the material flow ahead of the investment.
– Customers tend to try and rule out risks as much as possible. The ability to verify the feasibility of a multimillion-dollar investment up-front greatly boosts the readiness to place the order, he says. Without the Tecnomatix based feasibility study, we would likely not have won this and a number of similar orders.
Another benefit is that control software development can be accelerated considerably if engineers can concentrate on formulating methods and processes proven successful in simulation. This also helps avoid errors and the extra work for corrections. In turn, this not only reduces development cost but also the time required to implement complex projects and meet ever tighter de