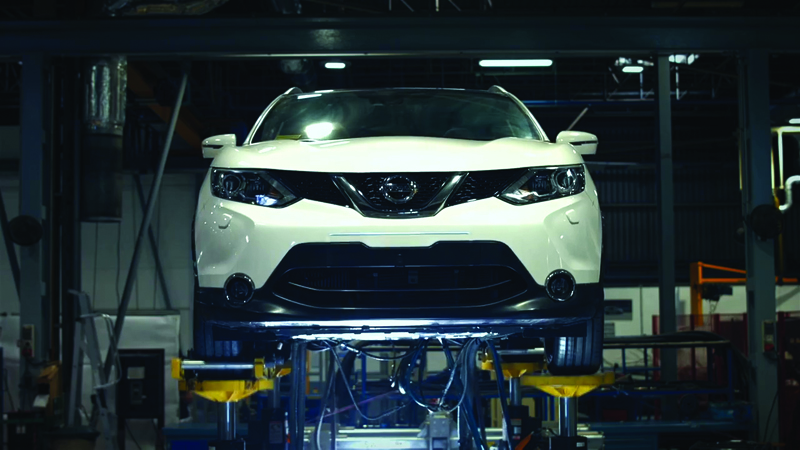
Nissan optimizes the durability of its cars using Siemens PLM Software solutions
Barcelona, Spain. In recent years, Nissan has enjoyed rising sales figures, establishing itself as a leading car maker. To strengthen the brand and optimize the quality of its vehicles even further, Nissan is aiming to develop cars with the longest possible service life and high reliability. To achieve this, the company opted for solutions from the Siemens PLM Software Simcenter portfolio for vehicle testing. Simcenter, the system simulation software suite with its 3D CAE and tests, has allowed Nissan to set up an efficient, test-based process for extending the durability of its vehicles. In addition to this, the Siemens solutions help the company to collect precise production and component data which is also used to optimize the vehicles.
In order to satisfy future customer needs and to increase demand further, Nissan relies on two key elements:
High quality and extended durability. For European customers, these two terms are almost the same thing. The primary task of the department responsible for this at the Nissan Technical Center Spain (NTCE-S) is therefore testing the vehicles and their components for their durability. In order to continuously improve the service life of the vehicles, NTCE-S has invested in the most up-to-date test software from Siemens. Simcenter allows the experts in Spain to set up an end-to-end solution for testbased durability engineering.
Flexible hardware
As the engineers have to transport the equipment for the tests to different test environments, they benefit from the compact design and flexibility of the Simcenter Scadas hardware.
– We use Simcenter Scadas for all our data acquisition tasks, says Arturo Barreu, Test Engineer in the Function and Durability Department at NTCE-S.
Beyond data acquisition, the team streamlined its vehicle durability engineering process by relying on Simcenter Testlab software for load and fatigue analysis. The software effectively supports every step of a testing campaign, from data acquisition to load classification and fatigue life prediction.
All in one
All durability and NVH (Noise, Vibration and Harshness) data is acquired using the same Simcenter Scadas hardware, and the analysis is performed in a single software environment, making it a very efficient process for the engineering team.
– We are testing more and more electronic components and fewer mechanical parts. The collaboration with Siemens is essential to adapt to these changes and to validate these new components, summarizes Barreu.