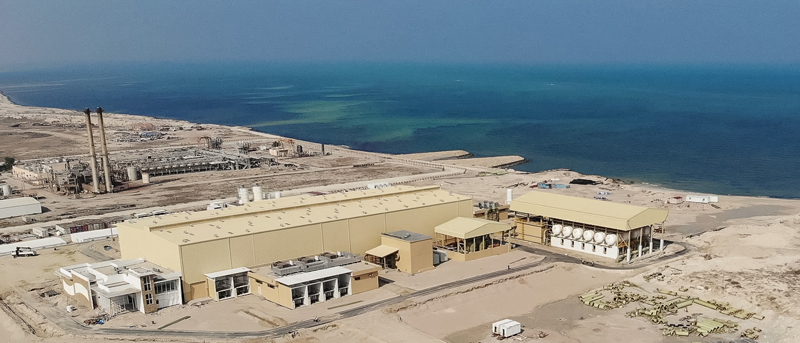
Siemens technology drives the world’s largest solar-powered plant for extracting drinking water
Al Khafji, Saudi Arabia. The water desalination experts Rawafid Industrial and Advanced Water Technology (AWT) have built an ultra-modern plant for extracting drinking water on the coast of the Arabian Gulf in response to demand for a reliable supply of drinking water for a growing population. Sea water is processed here in a two-stage, solar-powered reverse osmosis process to produce fresh water. Some of the key challenges involved in the project included the tight schedule and the capacity of the plant – up to 90,000 cubic meters of water can be processed here every day. Rawafid Industrial relies on Siemens solutions for the electrical equipment, automation with integrated drive technology, communication, and instrumentation. Efficient use of solar energy significantly reduces the carbon dioxide (CO2) emissions from the plant compared to plants using electricity from non-renewable sources. In addition to this, the Siemens technology ensures a plant availability of approximately 98 percent.
Reverse osmosis – this is the term given to a process which allows fresh water to be extracted from saltwater. The most important component of the process, apart from seawater, is electricity. A great deal of electricity. Using this method to extract drinking water is therefore extremely expensive and also produces a great deal of carbon dioxide (CO2). However, a new approach is being taken in Saudi Arabia by using an almost inexhaustible energy source: The sun. Together with experts from Advanced Water Technology (AWT), Rawafid developed a solar-powered water extraction plant with a capacity of up to 90,000 cubic meters per day. This ambitious project was completed within 14 months which is attributable to no small degree to the close and smooth collaboration with the supplier for all the electrification, automation, drive technology, communication, and instrumentation technology – Siemens.
End-to-end solution with standard components
The new plant is based on a twostage reverse osmosis process. The physical process utilizes pressure to reverse the natural process of osmosis to concentrate substances dissolved in the fluid – in this instance, salt. Power is received from a neighboring solar power plant with a connected capacity of up to 20 megavoltamperes (MVA). During the night, the plant is powered through the public grid. Siemens supplied an end-to-end solution comprising Sitrans process instrumentation and components from the Scalance portfolio for reliable network communications, as well as Sinamics GH180 and G150 converters for secure operation of the plant, Sivacon switchgears, and Siprotec to protect the digital substations. The process automation is operated by the distributed control center Simatic PCS 7 enabling high flexibility and reliability of all processes.
– The system is not dedicated to a certain specific process, and it is not customized. We can adjust all the parameters by ourselves without calling Siemens for changes in the software, enthuses Ali Awadallah, CEO and project director at Rawafid. It was also possible for Rawafid to significantly modify the project thanks to the experience of their partner, Siemens, for example, changing the energy supply from 34.8 to 13.8 kilovolts. The Siemens solution also allows simple vertical and horizontal integration of all the electrical components which significantly reduces operational and maintenance costs.
Achieving more together
Since its commissioning, the plant has been running without a hitch and with an availability of 98 percent, producing even better-quality water than expected. By reducing the operating costs and CO2 emissions, this modern plant shows how efficient reverse osmosis can be. The project director’s summary is equally positive:
– I would state that you could hardly get a better partner. With Siemens, it is engineer talking to engineer – you understand each other, and that is what makes a project a success. We always want to achieve the best result in the project, and we can achieve this with Siemens.