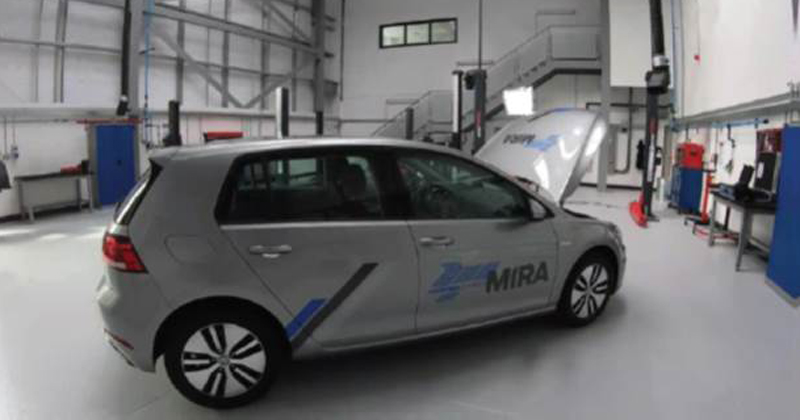
Automotive engineering consultancy uses Simcenter testing to assess the sound quality of electric vehicles
Siemens Simcenter helps HORIBA MIRA provide its customers with noise, vibration and harshness performance enhancements
Measuring noise, vibration and harshness
Electric vehicles represent a huge step change in terms of measuring acoustic performance, also known as noise, vibration and harshness (NVH). This is a particular challenge for automotive engineers who have spent years assessing internal combustion (IC) engines. As Mark Randle, NVH Team Leader at HORIBA MIRA, explains:
– There are specific difficulties around the assessment of noise, vibration and harshness in electric vehicles. Whereas an internal combustion engine generates obvious low-frequency noise, the motor within an electric vehicle creates higherfrequency noises which are often less pleasing to the human ear. At the same time, any noise coming from the road surface or from wind is more noticeable to the driver and passengers and affects their perception of auditory comfort.
Mark Burnett, technical lead for the noise and vibration attribute, expands on this point:
– In a car with an IC engine, the harmonics increase in frequency as the vehicle accelerates. These harmonics provide useful feedback to the driver, but they become a nuisance if they are too loud. An electric vehicle will also emit harmonics, but they tend to be higher orders and are often perceived as less pleasant whines. This results in a compromise; we want to give the driver feedback, but we do not want these whines to be too prominent over the background road and wind noise. A balance has to be achieved.
With an automotive reputation that goes back more than 70 years, HORIBA MIRA has the relevant experience and expertise to tackle such contemporary industry challenges. The company is well known for its proving ground, test facilities and engineering consultancy services. As Nick Fell, engineering and technology director, notes:
– The great value we add is to understand and define the targets that our customers and end users require, then devise technical solutions that deliver those attribute requirements.
A member of the HORIBA Group, based in Japan, HORIBA MIRA has 650 full-time employees and revenues of £65 million per year. Its international customer base ranges from ambitious start-ups through component suppliers to globally established vehicle manufacturers.
Understanding sound and its origins
The NVH department at HORIBA MIRA undertakes extensive analysis of the level and quality of sound within different types of vehicles. Transfer path analysis (TPA) is one of the fundamental techniques used to measure interior noise and vibration and break these down into contributory paths. When microphones and vibration sensors are fitted to a car, it is possible to measure the frequency response of the structure at different speeds and identify their exact source.
– Noise and vibration reach the driver either through the structure or through the air, notes Randle. It is important to understand the exact route because we can then make design recommendations to our customer if necessary.
Specialist software and hardware is critical for this type of work and HORIBA MIRA has been using the Siemens Simcenter testing solutions for more than 25 years. Simcenter Testlab software and Simcenter SCADAS hardware are a complete solution that includes an extensive range of tools that can be used to identify loads and obtain transfer functions and operational data.
– The Siemens solution is part of our offering, says Randle. The capability it gives enables us to be more efficient, from design through simulation to validation. With our license model, we have access to a rich and wide range of methods, both for acquisition as well as processing of the data. This allows us to select the best methods for different needs. Thanks to this licensing model we have an extensive range of powerful software available to us.
Burnett uses Simcenter Testlab on a daily basis. – Through signature testing and analysis, we can acquire operational data from a vehicle and separate out the higher frequency orders that tend to be present in an electric vehicle, even in the presence of background noise, Burnett says. – The spectral test and modal analysis applications enable us to understand the various resonances within a structure and measure the required transfer functions with different excitation techniques. Using this data we can assess whether making a design change, such as stiffening a component, would reduce a vehicle’s interior noise. Finally, the desktop reporting feature provides a straightforward and convenient method of visually presenting and interrogating data.
Expanding technical capability
In line with its ethos of continuously developing its capability, HORIBA MIRA undertakes independent research as well as customer-focused investigations. On a recent project the company purchased a commercially available electric car so that it could fit it out with instrumentation and conduct extensive analysis. – We set out to deepen our understanding of electric vehicles and validate the TPA process using the Siemens solution by working with a Volkswagen e-Golf, Randle explains. This TPA exercise allowed us to quantify and rank the structure-borne noise contributions through the motor mounts, the driveshafts and the airborne noise radiated from the motor itself.
– At HORIBA MIRA, a lot of our work is focused on developing prototype vehicles and when we first take delivery of them it is quite straightforward to make improvements using relatively simple techniques, Burnett adds. As the prototypes mature we need to use more detailed methods, such as TPA, to make further improvements. It was therefore very useful to focus on a car of such caliber; the project confirmed that we can achieve very strong correlation even with a quiet electric vehicle.
Ensuring efficiency and reliability
– The instrumentation and physical testing involved in TPA are time consuming, Randle notes. However, the process delivers significant data and with Simcenter Testlab we have data acquisition combined with data processing on one platform. That means we obtain instant results when we are out testing on the track and can make immediate decisions to move the development process forward efficiently.
– It’s one thing creating a software that is mathematically correct, that is a given, Burnett says. It’s far more difficult to design a piece of software that can be implemented effectively within a commercial environment and, with Simcenter Testlab, Siemens has done that very well.
– Electrification, alternative fuels and autonomy are increasing the complexity of vehicles, Fell observes. It is impossible to physically test every use case and, although we expect physical testing to increase, we expect simulation to grow even more quickly. That is why the validation of simulation models is extremely important. Our use of Simcenter SCADAS hardware for data acquisition means that we can efficiently measure the NVH behavior of vehicles, cross-check with simulation results, make reliable recommendations to our customers and ensure that we maintain our leading role in the marketplace.