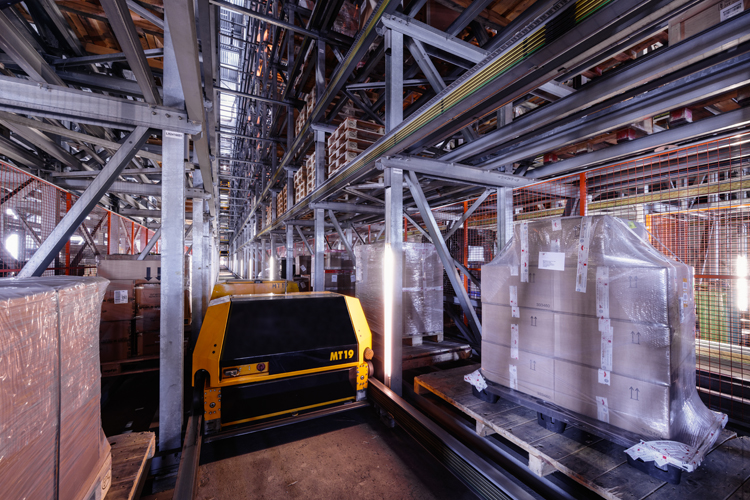
Logistics specialist uses fully automated storage logistics and tech from Siemens
Zürich, Switzerland. Zürich Airport turns over more than 1300 tons of freight every single day. Logistics specialist Cargologic is in charge of ensuring everything runs smoothly and reliably. The company uses fully automated freight lifts and high-bay warehouses for interim storage and preparation of the goods for onward transport. Given this volume of freight, it goes without saying that the warehousing logistics systems and infrastructure in place have to work reliably, so Cargologic opted to use storage system controllers and drives from Siemens. Not only does the integrated solution in place ensure the easily manageable stocking of spare parts, the Siemens solution is also lighter in weight than the previously used drive system, which was mounted above the lift and difficult to access.
The new system permits a significant weight reduction and is more accessible, enabling simpler handling and component exchange should repairs be required. Roses fresh from Ecuador or medicines from the USA – all the goods arriving into Zürich Airport are unloaded and stored ready for onward transport by Cargologic. The company has 8000 pallet rack locations available for interim cargo storage. The entire contents of the high-bay warehouse are turned over once a day. The process never changes: The bar code of each pallet is scanned as it enters the warehouse. The pallets are transported around the clock to their target destination using consignment lifts, Manitracs (fully automated carts on rails) and Manitrac lifts. To prevent unscheduled downtimes, Cargologic relies on Siemens solutions for the drive and control technology used in its lifts.
Two lift types, one system
Depending on their field of application, the lifts are designed to carry loads of 1.5 or three tons. They require motors which, despite their ability to handle heavy loads, should be intrinsically light in weight to enable easy access in case of repairs. The Siemens solution enables a compact Simotics IPH8 asynchronous motor and its H2DH09 Flender gear to be independently transported per lift cab. Each assembly weighs no more than around 820 kilograms, making this a true lightweight solution in comparison to its predecessor, which tipped the scales at 4.5 tons each. The significantly smaller size of the new components additionally simplifies any exchange or inspection work. The motors are controlled by Sinamics S120 drive systems and Simatic S7 controllers. Although the warehouse uses two different lift types carrying different loads, the same components can be used in both. The benefits are evident: this solution not only simplifies maintenance and servicing but also helps to significantly streamline the stocking of spare parts.
The work continues
Conversion of the first of a total of twelve lifts is already completed, with more set to follow over the course of 2019. Those in charge at Cargologic are delighted with the project’s progress so far, and are undaunted by the prospect of the ongoing conversion work:
– Siemens has the necessary resources behind it. If anything doesn’t work as it should, there will be specialists on site in no time to sort it, says Cargologic’s Technical Director Urs Stupler.