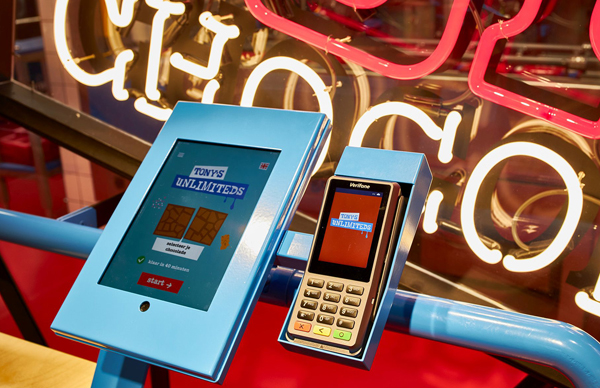
Siemens automation allows serial chocolate production in batch size 1
Amsterdam, Netherlands. In Tony’s Chocolonely Super Store (Tony’s), chocolate lovers get maximum value for money. Behind the ‘sweet façade’ Tony’s is running a highly professional, high-tech operation. This is reflected in the fully automatic chocolate machine, called Tony’s Unlimited, which is on display in the shop window.
Customers can send orders to the machine from a tablet and then have their customized chocolate in their hands 40 minutes later. The ‘Unlimited’ part of the name refers to the fact that customers can choose from the total of 20 ingredients and then configure their packaging. Tony’s Unlimited is controlled by technology from the Siemens Simatic portfolio.
This allows not only highly-flexible serial production in batch size 1 but also efficient engineering and comfortable plant operation. Anyone visiting the shop in Amsterdam will find themselves in a world of chocolate – not just exquisite varieties of this sweet confectionery but magazines and books on the subject as well. You get the feeling that the owners are deeply in love with chocolate. And there’s more. Sourcing sustainable and fair ingredients without, for example, child labor or wage dumping is also very important to them, something which is 100 percent in evidence at Tony’s. Customers spending their money here should ideally share or give away not just the chocolate but the story behind it as well. To this end, Tony’s came up with a unique marketing initiative – Tony’s Unlimited, a machine which produces customizable chocolate bars. And all controlled by a Siemens Simatic S7-1200.
Everything under control
The machine, manufactured by Hacos, does more than just produce customizable chocolate bars. It also packages them in what is called two-in-one packages: One bar is for the purchaser, the second should be given away, thus spreading the philosophy of the business. At the heart of the plant is a Simatic S7-1200 Basic Controller which receives the recipes based on the relevant order and forwards this data together with the current status to the RFID (Radio Frequency Identification) tags on the molds. A Simatic controller then provides the current relevant data such as the production status and monitors the cooling process.
Once the bar is ready to pack, the Simatic sends a signal to the store system. The complex yet compact automation is operated by several pre-configured and ready-to-use Simatic HMI (Human Machine Interface) Comfort Panel Pro units. The TIA (Totally Integrated Automation) engineering framework makes the engineering particularly easy.
Optimum solutions to challenges
The demands on Tony’s Unlimited and the process behind it were considerable. The melting line and cooling process located at the rear of the shop can be viewed by customers and must not only be visually appealing but also extremely compact. This also applies to the automation, control and visualization components.
The line must also be highly flexible and able to produce chocolate bars to individual customer specifications within a short period of time. The automation captures each order and checks that the user knows exactly where each chocolate bar is in the process. As the plant is also integrated into an order, tracking and checkout system which was developed specially for Tony’s, the Siemens automation technology also uses open interfaces for seamless integration and real-time data transfer. In the end, Hacos succeeded in creating a plant for serial production in batch quantities of one which can run 24 hours a day. The Simatic controller ensures reliable data transfer and the Comfort Panels provide simple and user-friendly operation