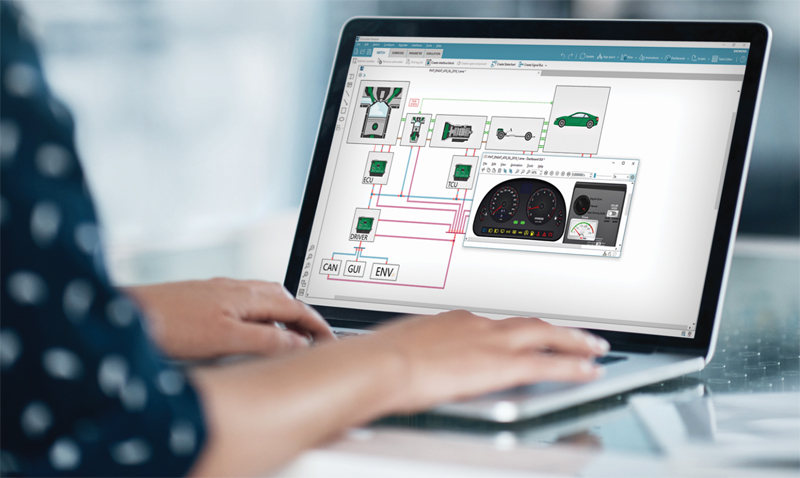
New simulation solution brings applications together and makes handling easier
Plano, USA. Siemens Digital Industries Software presents the latest addition to its portfolio: the new Simcenter system simulation solution. This simulation software supports industrial companies in the creation of precise system modeling which is both costefficient and competitive. Simcenter System Simulation combines Simcenter Amesim software, a simulation platform for mechatronic systems, and Simcenter Flomaster, a vertical solution for thermo-fluid systems of any size and complexity. With this pooled solution users benefit from increased user-friendliness and openness for their applications. The simulations with Simcenter also make it easier to develop new products.
The new solution is ideal for applications in the automotive, aerospace, marine, energy and utilities industries.
Companies can benefit from enhanced modeling functions for mechatronic and thermo-fluid systems in order to manage complex modelling processes efficiently. Simcenter system simulation also offers the opportunity to optimize electrification, which helps to assess the electromechanical performance of applications and the thermal behavior on driving cycles more accurately. In version 2019.2, Simcenter system simulation solutions offer an improved user experience, more scalability and reduced processing time on modelling, as well as increased openness and interoperability.
Siemens expands additive manufacturing portfolio through acquisition of Atlas 3D
- Atlas 3D helps designers define optimal part orientations for ‘right first time’ 3D printing
- Cloud-based, GPU-accelerated Sunata software can reduce downstream 3D printing errors caused by thermal distortion up to one hundred times faster than other solutions on the market
Siemens announced today that it has signed an agreement to acquire Atlas 3D, Inc., a Plymouth, Indiana-based developer of software that works with direct metal laser sintering (DMLS) printers to automatically provide design engineers with the optimal print orientation and requisite support structures for additive parts in near real-time. Atlas 3D will join Siemens Digital Industries Software, where its solutions will expand additive manufacturing capabilities in the Xcelerator portfolio of software.
Sunata software uses thermal distortion analysis to provide a simple, automated way to optimize part build orientation and generate support structures. This approach allows the designer—rather than the analyst—to perform these simulations, thereby reducing the downstream analysis that needs to be conducted via Simcenter™ software to achieve a part that meets design requirements. Siemens plans to make the Atlas 3D solution available through its online Additive Manufacturing Network.
– We welcome Atlas 3D to the Siemens community as the newest member of our additive manufacturing team. Our solutions industrialize additive manufacturing for large enterprises, 3D printing service bureaus, design firms and CAD designers, said Zvi Feuer, Senior Vice President, Manufacturing Engineering Software of Siemens Digital Industries Software. – – The cloud-based Sunata software makes it easy for designers to determine the optimal way to 3D print parts for high quality and repeatability. The combination of Sunata with the robust CAE additive manufacturing tools in Simcenter enables a ‘right first time’ approach for industrial 3D printing.
– Siemens is a leader in additive manufacturing, with the most integrated and functionally robust solutions in the industry, so we are excited to join the team, said Chad Barden, Chief Executive Officer of Atlas 3D. – The power of Sunata is that it equips designers to more easily design parts that are printable, which helps companies more quickly realize the benefits of additive manufacturing. As part of Siemens, we look forward to introducing Sunata to customers who already have Siemens’ AM solutions and can achieve new efficiencies in their front-end design-for-additive process, as well as companies who have yet to start their additive manufacturing journey.
The high rate of 3D print failures is a key challenge companies face in leveraging additive manufacturing for high-volume production. Parts often need to go through several design and analysis iterations before the optimal build orientation and support structures are determined. Typically, designers don’t have the capabilities to consider such factors as part orientation, distortion, and heat extraction uniformity in their design. This puts the onus on engineering specialists to resolve such issues.
Atlas 3D’s Sunata software solves this problem by giving front-end designers a quick, easy and automated way to get much closer to a “right first time” build. Sunata is a GPU-accelerated high-performance computing additive manufacturing software solution that can deliver results up to one hundred times faster than other build simulation solutions on the market. GPU-accelerated computing is the employment of a graphics processing unit (GPU) along with a computer processing unit (CPU) to facilitate processing-intensive operations such as deep learning, analytics and engineering applications.
With Atlas3D, designers and manufacturing engineers can quickly gain insights into the optimal part build orientation in order to minimize supports, distortion, effort to remove supports, part material, and printing time.