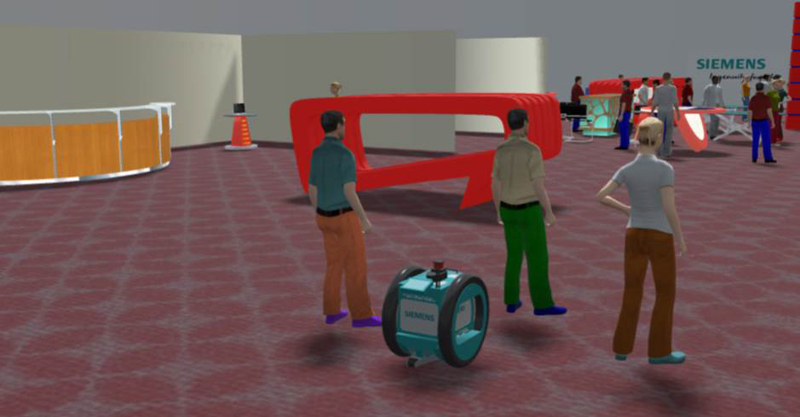
Droid delivery manufacturer uses Simcenter software to validate advanced safety mechanisms
Siemens Digital Industries Software solutions enable TwinswHeel to save time and costs by streamlining technical choices, development and verification.
Seeking a sustainable solution
Autonomous driving has been at the center of attention and innovation in the automotive sector for the past five years and this continues to be the case. With urban populations rising, movement of people and goods in big cities must be reconsidered. Indeed, online shopping growth plays a role in traffic issues and raises logistical concerns with new regulations and traffic restrictions. The challenge of last-mile delivery is therefore being taken up by many manufacturers. It is considered the most expensive and time-consuming part of the delivery process and needs to be addressed more efficiently.
Delivery drones and robots offer sustainable last-mile delivery solutions that are generating growing investments. Indeed, MarketsandMarkets predicts the autonomous last-mile delivery market will be worth $91.5 billion by 2030, which is supported by a McKinsey report that mentions some organizations are forecasting 80 percent of last-mile deliveries will be autonomous by 2025.
Contributing to future urban logistics After studying the market and the demand for this new form of delivery, TwinswHeel, a French startup founded in 2015, decided to design a robot that could negotiate city traffic restrictions and receive acceptance in cities. First, they developed the service for enclosed sites such as large factories and warehouses and semi-open sites such as hospitals and shopping centers. Now they are working at a larger deployment in the city of tomorrow to deliver e-commerce parcels or help craftsmen and people with disabilities carry their loads. Their goal is to design and manufacture droids that will contribute to future urban logistics. TwinswHeel’s droids can move in two main modes: collaborative mode called follow-me or in 100 percent autonomous mode.
Coming from the automotive industry, Vincent Talon, chief executive officer (CEO) of TwinswHeel, says it was an obvious decision to create something with wheels to partially fulfill the role of a car. The first prototype had only two big wheels, but to stay competitive they adapted the architecture and created a platform with four wheels, which is closer to automotive and thereby provides benefits of scale.
– The development of our robots is guided by three main concerns: design a safe and reliable vehicle that meets customer demands, keep acquisition and ownership costs under control and shape an object that will generate empathy and therefore public acceptance, says Talon.
To develop a technologically competitive robot, the TwinswHeel founders have gathered a team of 12 engineers, and since the beginning of the development of their robot, TwinswHeel more than doubled their staff with dedicated engineering divisions for mechanical, electrical, controls and sensors integration domains.
Safety first
After entering the mature and competitive industrial market, TwinswHeel’s objective was to offer a new service in urban environments.
This droid is a great example of a new zeroemission service. In the city of Toulouse, France, it is used to assist Enedis power grid agents who repair the electrical network downtown, so they no longer enter the city with a van. On the other hand, Franprix Supermarkets uses the robot to help elderly or disabled people carry their groceries. Autonomous droids are currently being tested in Montpellier, France with La Poste (the national mail service) and STEF (European leader in refrigerated transport)
However, with these new applications, safety becomes the number one priority. Even if there are not yet regulations for operating these kinds of robots without human supervision, experiments are planned for 2020. TwinswHeel is working closely with the French government to create these regulations and has been enrolled in pilot projects aimed at analyzing the acceptance level.
So currently, TwinswHeel’s droids are required to meet the same safety levels as an autonomous car.
– We have a greater sensitivity to safety than our competitors, says Talon. We respect the standards of motor vehicles because we consider the droid an autonomous vehicle.
The engineering team had to implement validation plans to check safety requirements. But these plans require millions of runs that are physically impossible to do. The inherent software and hardware complexity, the required massive validation and verification cycles and the growing number and variety of sensors require manufacturers to rethink their development processes. Simulation has become the indisputable innovation enabler for the development of autonomous vehicles. In this realm, the Simcenter™ software portfolio provides solutions and services to enable multi-domain designs exploration, verification and validation for the development of autonomous vehicles at a systems, software and full-vehicle level.
– We use Simcenter Amesim and Simcenter Prescan for model-in-the-loop tests to simulate the last developments and verify the requirements defined upstream are met. It takes less time and money than doing it on a real vehicle, explains Talon.
Sense-think-act
The engineering of an autonomous vehicle requires developing and validating complex sense-think-act functions. This requires an integrated system of systems, with mechanical, electrical and software components. For an optimized design, these components cannot be treated as separate elements, and software and hardware need to be developed in sync to achieve required hardware costs and system performance.
During live experimentations, the droid identifies and encounters many hazardous situations. Information is collected so the user can recreate the same situation virtually or generate a hypothetical one based on expert knowledge. When a critical situation occurs, the last 30 to 60 seconds of all robot sensors data is saved. This information is then used to create a re-useable and configurable Simcenter Prescan™ software simulation scenario.
– Having those scenarios reproduced in a simulation environment using Simcenter Amesim and Simcenter Prescan allows us to build a catalogue of critical case scenarios for validation plans or future developments. The main advantage we find is these scenes are reproducible, leading to much easier iterative work, notes Talon.
Integrating multiple complex technologies
– Many physical domains had to be combined to propose a reliable, robust and functional product to our customers, says Talon.
Indeed, the droid is equipped with two electric motors, a rotative 360-degree lidar for simultaneous localization and mapping, a stereo camera for target identification and obstacle avoidance and ultra-sound sensors for detailed mapping of close obstacles. Everything is manufactured and assembled internally, except the sensors.
– We use Simcenter Amesim to build models that enable us to select the vehicle architecture – for instance, to size the electric motor – as well as models to design and validate robot controls and for supervisors of artificial intelligence supporting decision-making processes for droid movements, Talon says.
Using system simulation, startups can develop their solutions quickly by testing multiple variants and choosing the option that meets their needs. They can develop first models when little data is available in order to make first architectural choices, and then when suppliers are selected, it’s possible to build more complex models, including mechanics, electronics and electrics. It enables companies to have complete models for sizing and controls design.
– Simcenter Amesim is the optimal software for multi-domain modeling, says Talon. – It allows us to combine the different physics of the robot and provides robust solutions, enabling us to move forward rapidly.
The decision part of the robot is the most complex system. To integrate the sensors, TwinswHeel uses a robot operating system (ROS) that enables it to get the sensors’ drivers and plug them in with the rest of the software. ROS is a network that allows different software components to communicate, whether they are in C, Python, Matlab environment, etc. TwinswHeel creates nodes (software components) in the ROS that can exchange information like the lidar point cloud. Calculating autonomous displacement of the robot’s perception, tracking the master in follow-me mode, localization, path planning and control of the trajectory is carried out in these nodes.