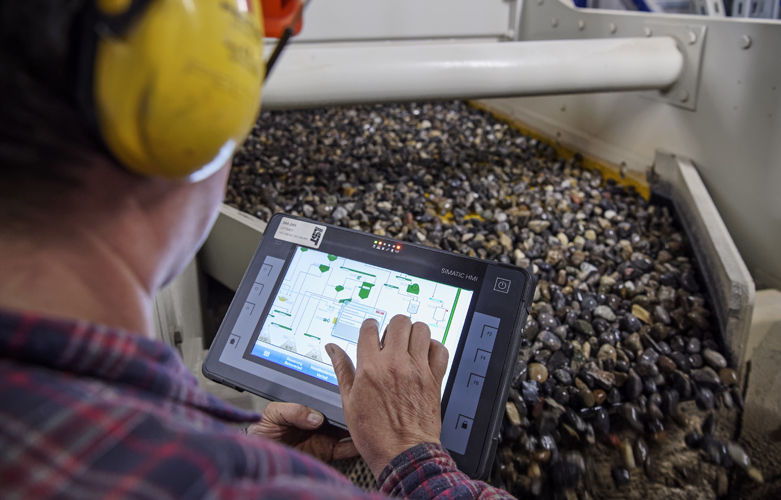
Swiss building material company modernizes plant with Siemens digitalization components
Birr, Switzerland. Kibag AG is a leading player in the building material and construction sector and operates multiple gravel and cement plants, building companies, and recycling and waste-disposal companies. At the gravel and cement plant in Birr, the company excavates around 230,000 tonnes of gravel every year. In order to improve efficiency and at the same time make better use of resources and personnel, Kibag relies on digitalization.
The company also modernized the whole plant in Birr in 2018 using components from the Siemens portfolio. As a result, machines, conveyors, breakers, and loading stations can now be controlled from a tablet and plant disruptions can be easily and quickly resolved. This makes the Birr production facility one of the most up-to-date and efficient of its kind. This is how it used to be: One employee located at the control center, and employees with radios who were supposed to understand the instructions from central while surrounded by deafening noise levels. It goes without saying that this is not efficient, let alone beneficial to health. Kibag also recognized this which is why the company completely modernized its plant in Birr, turning to Louis Stuber AG (Stuber), a Swiss general contractor in the fields of electronics, building services, and industrial installation. Stuber quickly identified that a stable and reliable control and communications infrastructure would be required to digitalize the plant which is why they turned to the experts on Siemens technology from the Scalance and Simatic portfolio.
Coordinated control and communications technology
Stuber installed three new control cabinets to remove the material by loading it onto trucks and railway wagons, and to feed the cement plant. These cabinets contained not only the motor circuit breakers, Sinamics frequency converters and Sirius soft starters but also two fail-safe Simatic S7-1500 Safety CPU (Central Processing Unit) controllers. They are supplemented by local ET200SP I/O systems. The soft starters prevent damage to the drives by providing the machines with a smooth start and also damp out voltage spikes from the mains. A WinCC Professional Scada (Supervisory Control and Data system) visualization system and a Simatic IPC547G industrial PC acting as a server provide the visualization. This allows employees to see at a glance the current fill levels or which conveyor is in operation. An ITP1000 tablet PC and two W786 Scalance access points provide mobile operation. The whole automation was completed in Version 15 of the TIA (Totally Integrated Automation) engineering framework portal.
Production resumed in record time
In addition to integrating the new components into the existing system, a further challenge for those involved in the project was to keep the down time for the refurbishment and modernization to an absolute minimum. The basic requirement was exceptional planning – planning which included, for example, simulation of the Simatic S7 PLCSIM in a test environment. – The Industrial Engineering Department at Kibag had prepared their scheduling systems for the integration as best they could and the simulation provided us with the certainty that the systems would interact as required. This allowed us to take on the extremely tight commissioning deadline, remembers Stuber’s Lukas Buri. Just in terms of numbers, this means that the plant was operational again after only two weeks and the team was able to complete the project within the estimated deadline.