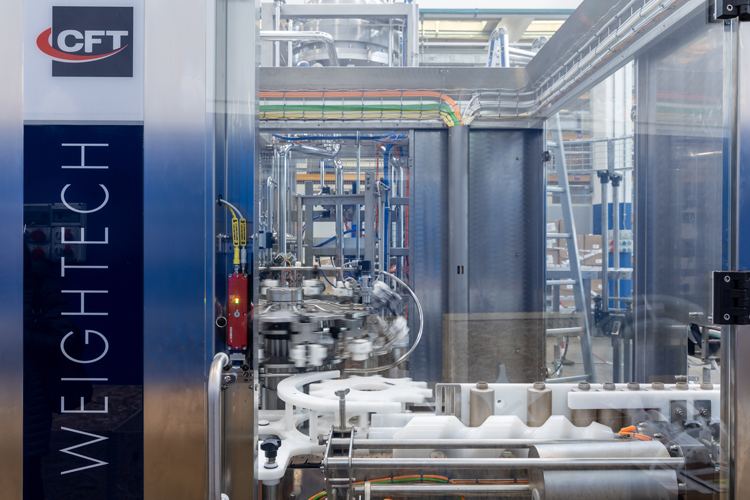
Plant builder relies on Siemens motion control for in-operation maintenance
Parma, Italy. The CFT Group designs and builds production lines and turnkey systems primarily for the food and beverages industry. One of its customers, Menz & Gasser, which specializes in producing and packaging preserves and honey in portions for hotels, restaurants and catering, had CFT develop a rotary filling plant to a very high specification. The plant was to meet strict safety requirements and increase production capacities, while being exceptionally user-friendly. Key elements were extremely easy maintenance of the machines, ideally during operation. To achieve this, CFT turned to motion control solutions from the Siemens portfolio. This ensured that not only were the customer’s strict safety requirements satisfied but the cost for planning and commissioning each individual machine could be reduced by approximately 30 percent due to the Siemens technology.
Most people know them from in-flight food or breakfast buffets in hotels – small, neatly packaged portions of preserves and honey. The Italian company Menz & Gasser specializes in working with these small fill quantities. One of the key factors in the filling process for Menz & Gasser is safety – for both plants and employees. This is particularly important when employees, for example, have to have access to the interior of the machines during the filling process for monitoring or maintenance purposes.
– It is very important for us that we provide a guarantee to operators that they can work safely when the protective enclosure is raised, explains Ruggero Zanco, responsible for industrial automation at Menz & Gasser. And the use of up-to-date solutions from Siemens is the primary reason the company can meet this requirement.
Up to 30 percent cost saving
The basic precondition for safe intervention is precise throttling of the speed and control of the torque.
– It is not only parts moving within the machine that pose a danger but also the liquids used to clean and sterilize it, says Filippo Tedeschi, Filler & Seamer Automation Manager at CFT. The CFT experts therefore turned to the extended functionalities of the Siemens Simotion motion control system to complete this demanding task. The motion control ensures that not only do all the axes inside the machine come to a complete standstill when an operator intervenes but that they also retain their position and start up again quickly and efficiently once the work is finished. Project planning is carried out in the TIA (Totally Integrated Automation) Portal engineering framework.
– Thanks to TIA Portal and its associated software solutions and diagnostic tools, we have succeeded in reducing the working hours for planning and commissioning by approximately 30 percent for each individual machine, enthuses Tedeschi.
The next step – up into the cloud
Tedeschi can see potential and benefits from the installed Siemens technology in areas other than just commissioning.
– The expanded diagnostics mean we can offer a significantly more efficient after-sales service for our customers for both test runs and customer service itself. CFT is also using the condition monitoring system for predictive maintenance and is now planning the next steps according to Tedeschi. – The next project we would like to work together with Siemens on is using its Mind-Sphere cloud solution. We want to increase the effectiveness and efficiency of our performance even further by processing and monitoring the vast quantities of data our machines produce. This will allow us to improve our machine quality even further and launch more innovative machines into the market.